Like all Lodge seasoned cast iron pieces, USA Enamel starts in their Foundry. The enamelled Dutch ovens are made from an iron core, cast in the same Disamatic sand moulding machine they use for their skillets, grill pans, and more. From there, it goes through grinding and cleaning to remove gating, bumps, and sharp edges—all of which are normal in the sand moulding process. The rough iron pieces are then moved to their Enamelling Facility and cleaned one more time to prepare them for the hours-long enamelling process to come.
Applying the enamel to iron
The enamelling process starts with a frit, which is a glass powder that we add to a water-based solution to create a clay. This clay is aged in a temperature-controlled section of our Enamelling Facility, then added to a specialized pressure pot and transported to our spray booths. Air pressure turns the clay into a fine aerosol, which our spray technicians artfully apply to each piece of iron. “As much as this is science, there’s also art to it,” says Kevin Rusch, Enamelling Operations Manager. “Each piece being hand-crafted requires just the right touch to complete it to the high standards that we hold.” This is especially true in the spray booths, where the technicians have dialled in on a unique process that helps bring consistent, brilliant colour to each Dutch oven.
From there, the pots move down the enamelling line—their next stop is a dehydration oven, where they are cooked at a low temperature that removes all the water from the enamel coating, leaving behind a powder coating we call the bisque. After a quick dressing of the exposed iron rim, the ovens and lids make their way to the furnace.
Mastering the furnace
The heart of the enamelling facility
One of the focal points of our enamelling facility is a 45-metre-long furnace made of over 100,000 moving pieces. Designed in Italy, it’s one of only six in the world—and the only one of its kind in the United States.
The oven can reach up to 900˚C—though we don’t need to keep it that hot to fire enamel. It takes the pots 45 minutes to move through the furnace, during which time the bisque is fired into the bright, glossy, glass coating that makes each piece of USA Enamel centerpiece-worthy.
Once the cooked and cooled Dutch ovens are out of the furnace, they’re inspected by hand using our rigorous quality standards. Some don’t make the cut—and we take that as a point of pride. But those that do meet our standards are accented with stainless steel knobs and hardware—all by hand—and then packed into their cartons. We add pot protectors and a Use & Care booklet to each carton and then send the enamelled Dutch ovens to our distribution centre across campus.
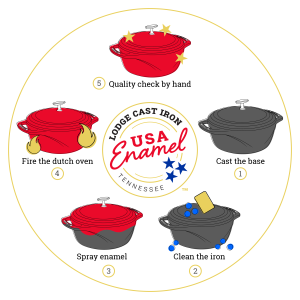